Application of a sheet of Oberflex laminate.
Installation of the panels must comply with the specifications outlined in NF T 54-320 the standard: ”Guide de mise en oeuvre des stratifiés décoratifs haute pression” (Installation guide for high pressure laminates).
Storage and handling
Store the panels with the decorated sides facing each other. Storing them flat is the best option. You can also store the panels vertically in specially designed racks to prevent them from sagging. It is recommended that the panels be stored in an enclosed area away from humidity. Make sure that the panels are handled with great care to avoid scratching and cracking of the resin. The best method is to have two people carry the panels in such a way that the decorative side forms the concave side.
Acclimation
Because their surface is made from natural wood, the panels work a little harder than traditional laminate panels. Before gluing, they must be perfectly acclimated. The best way of doing this is to store the panels and the substrates for 8 to 10 days in a room where the ambient conditions are as close as possible to those of the rooms where the panels will be installed (be particularly careful with overheated rooms without air humidification).
Normal conditions should be in the following range:
Temperature of 18° to 22° C.
Relative humidity: 50 - 60%.
Using a panel that is too humid may cause cracking due to shrinkage. On the other hand, a panel that is too dry may cause distortion (warping) or blistering in case of inadequate gluing. Acclimation is only really effective if air circulates between the panels during storage. On some substrates, if both sides are to be lined, one solution is to adjust the panels covering each side with the same hygrometric degree by stacking them on top of one another alternatively in the order and the direction of their use. Generally speaking, it is preferable to store them in a dry environment rather than one that is too humid.
Substrates
The panels can be applied on all common substrates (particleboard, MDF, plywood... except solid wood) that have a flat surface, and which are well degreased and dust free. Gluing on metal requires a careful preparation of the surface, in particular a good degreasing with a powerful degreaser (trichloroethylene, etc...).
Avoid applying on plaster or cement.
Balancing
To prevent a panel lined with an OBERFLEX- type laminate from warping, it is necessary to achieve symmetrical stress distribution. Using an OBERFLEX type laminate panel with the same thickness on both sides yields the best result.
Otherwise, in a more economical way, but without any guarantee on our part, balancing can be done by using a standard laminate of at least equal thickness (thickness varies depending on the species).
In the case where the panels are used in small widths for wall coverings and held rigidly by a fastening system or by a frame, it is possible to veneer only one side of an OBERFLEX-type panel. In that case, and without any guarantee on our part, the other side must be insulated from moisture and can be lined with a standard veneer painted, or coated with a vapor-proof lacquer or varnish.
Gluing
The surfaces to be joined must be solid, perfectly dry, clean and free of dust, sawdust and grease.
Gluing with a glue press. Press gluing is the safest method. In this case, use standard adhesives for laminated panels (vinyl glue, urea formaldehyde glue, etc.). When gluing with a hot press, do not exceed 60°C. Above this temperature, there is a risk of creating tensions which adversely impact how of the various elements hold together.
Gluing without press (for small surfaces only). There is a large number of adequate contact adhesives on the market. However, we recommend Agoplac and Pattex adhesives.
Gluing should be done at room temperature between 18° and 22° C and 40 to 60% relative humidity. Dry heat is helpful as cold temperatures delay the evaporation of solvents; too much humidity can cause detrimental condensation.
Description of the different neoprene adhesives to be used
a. high performance polychloroprene adhesive. This commonly used contact adhesive is generally suitable for most applications requiring very good bonding strength. We recommend PATTEX Super-Power, PANO-ASD and Super AGOPLAC adhesives.
b. Highly heat-resistant polychloroprene adhesive. This glue should be used whenever high heat resistance up to 120° C is required in addition to excellent mechanical strength. We recommend PATTEX SPECIAL (HENKEL), AGOPLAC NCP (LAMBIOTTE) and NEOPRENE GEL (SADER).
Adhesive application. Mix the adhesive thoroughly before use. Apply the adhesive in a sufficient and even layer on both sides to be joined using appropriate tools (serrated spatula, glue roller, short-haired brush, spray gun). Make sure that the layer is sufficiently thick at the edges. When applying the adhesive with a serrated spatula, application on the substrate and on the decorative laminate panel must be done in a perpendicular direction. Once the solvent has evaporated, the adhesive film should be visible and sufficiently thick, therefore, porous or highly absorbent surfaces should be coated several times. Pre-gluing may be necessary. Before joining the various elements, the two adhesive films must be dry to the touch (the adhesive must not be transferred). Follow manufacturer’s instructions regarding open time and flash time.
Note: A short evaporation time may lead to incomplete evaporation of the solvents (weakening of the bond). Too long a time will result in poor adhesion of the two films. Note: As direct surface gluing is a very delicate procedure, we recommend proceeding horizontally.
Gluing of "M1" CSTB panels
The glues recommended above are for our standard panels. For fireproof panels with a different underlayer and which are glued to fireproof substrates of different types depending on the manufacturer, we recommend contacting the glue suppliers to determine the product best suited to each particular case. Some glues recommended for standard panels cannot be used on fireproof panels.
Roller-pressing
Using a press roller yields results comparable to those attained with the press process. We recommend the Pattex roller, which is perfectly suited to this operation. Roller pressing should be done in both directions, from the center outward. More pressure needs to be applied on the edges. Apply strong pressure on the roller with your body weight.
Machining
Sawing, milling and drilling are done with all the machines commonly used for machining laminates.
Protecting the cutting edges
After trimming, the edge of the wood must be protected from air exposure in the direction of the grain (end grain) by using colorless varnish in order to achieve a homogeneous ageing of the wood and to prevent oxidation.
Cleaning glue residue
Vinyl glue stains (white glue) are water soluble and can be easily removed. Neoprene and urea formaldehyde glue stains (with separate hardener) should be removed immediately. If glue deposits have had time to harden on the surface of the panel, it will be difficult to remove them without destroying the finish of the panel, as they can only be removed with a sharp chisel.
Technical support
Our technical support staff is at your disposal and will be pleased to help and assist you for each particular use. The information given in this case, as well as the information contained in this document are given in good faith to users. However, we can only be responsible for the quality of our products.
Warranty
OBER guarantees the intrinsic quality of its panels as having the characteristics defined in this data sheet. It should be noted that slight surface irregularities and color variations are to be considered normal and do not constitute a defect, as we use real wood veneers. Due to their nature, the panels behave like any other wood, and discoloration from excessive exposure to sunlight or moonlight cannot be considered a material defect. In the event of a dispute, OBER's warranty and liability shall be limited to supplying unfinished panels to replace the defective ones at no charge.
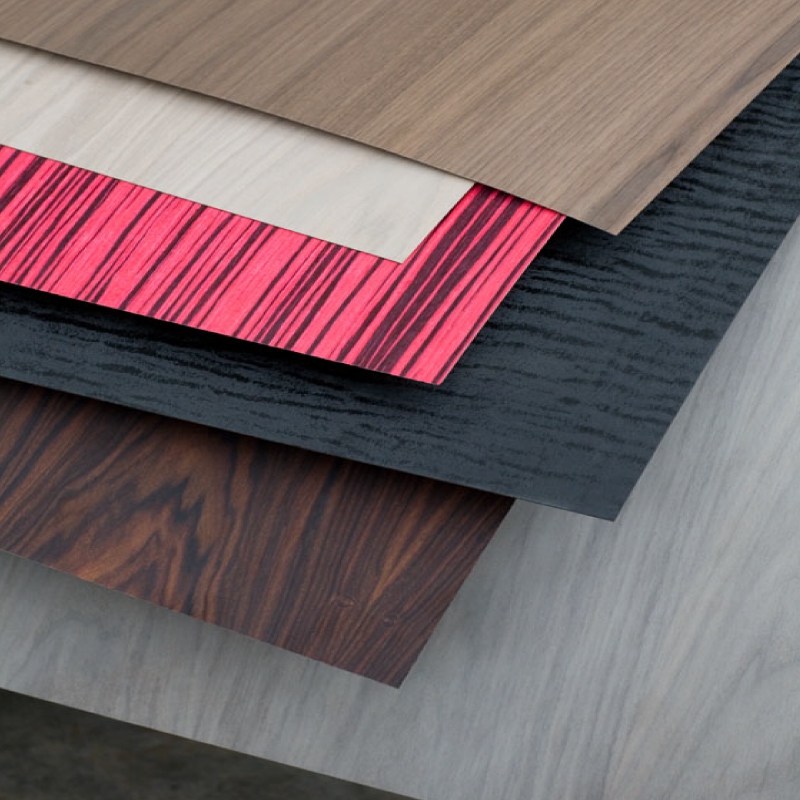